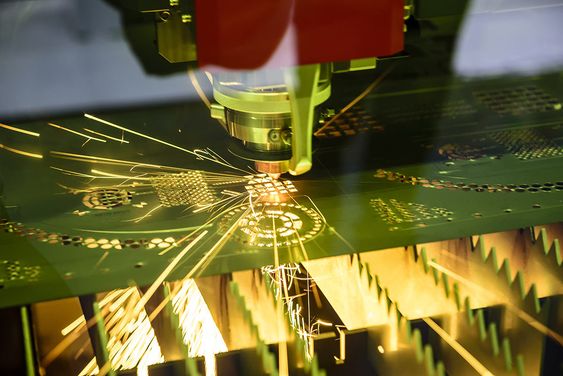
Laser cutting has become one of the most efficient and reliable methods for fabricating metal parts. Its speed, accuracy, and adaptability make it an essential process for businesses that demand consistent results and tight tolerances. As production demands increase across industries, manufacturers continue to turn to advanced methods like laser cutting sheet metal to meet quality and delivery expectations.
1. High Precision and Clean Edges
One of the primary reasons manufacturers rely on laser cutting sheet metal is its ability to produce highly accurate cuts with minimal deviation. The focused laser beam creates clean, smooth edges without the need for additional finishing in many cases. This level of precision is particularly valuable when creating intricate parts or working with complex geometries.
For industries requiring exact tolerances, such as medical devices or electronics, laser cutting delivers dependable and repeatable results. Clean cuts also help reduce the risk of product defects or misalignment in assembly.
Also read: https://www.weldflowmetal.com/what-makes-laser-cutting-a-versatile-solution-for-various-materials/
2. Faster Production Times
Speed is a major advantage of using laser cutting in New York or any other high-demand urban center. The ability to cut quickly without the need for tooling changes allows for rapid prototyping and short production cycles. CNC-controlled laser systems can execute complex cuts faster than traditional machining or manual cutting methods.
With minimal setup time and reduced interruptions, manufacturers can respond to customer demands more efficiently. This is especially useful in contract manufacturing environments, where time-to-market plays a critical role.
3. Versatility with Different Metals and Thicknesses
Laser cutters handle a wide variety of metals, including stainless steel, aluminum, mild steel, and copper. Thickness is also not a major limitation, as modern machines can adjust beam intensity and cutting speed based on material type.
This flexibility makes sheet metal cutting services that use laser technology a practical solution across sectors. Whether cutting components for HVAC systems, light fixtures, or enclosures, the method supports diverse materials and specifications.
Also read: https://www.weldflowmetal.com/six-ideal-metals-for-superior-results-in-laser-cutting-services/
4. Reduced Material Waste
Laser cutting systems follow digital design files with high precision, reducing the risk of human error and miscuts. The ability to nest parts closely on a single sheet maximizes material usage and minimizes scrap.
Less waste not only helps reduce material costs but also supports sustainability efforts. For businesses with high-volume production, this efficiency can result in substantial cost savings over time.
5. Seamless Integration with Digital Design Tools
Modern fabrication processes depend on CAD and CAM tools for design and programming. Laser cutting sheet metal integrates easily with these platforms, enabling smoother transitions from concept to production. Design modifications can be quickly implemented without altering physical tooling.
This digital compatibility supports rapid iteration, making it ideal for prototyping and small-batch production. For engineers and production teams, it improves communication and reduces delays.
Precision, Efficiency, and Flexibility with Weldflow Metal Products
Laser cutting continues to transform how manufacturers approach metal fabrication. Its speed, accuracy, and adaptability make it an ideal choice for industries that demand performance without compromise.
Weldflow Metal Products offers advanced sheet metal cutting services, including laser cutting, in New York to support industries with high-precision needs. Backed by decades of experience and cutting-edge technology, Weldflow helps clients achieve efficient, reliable results.
Need laser cutting sheet metal services for your next project? Contact Weldflow Metal Products to discuss custom solutions today.
Also read: