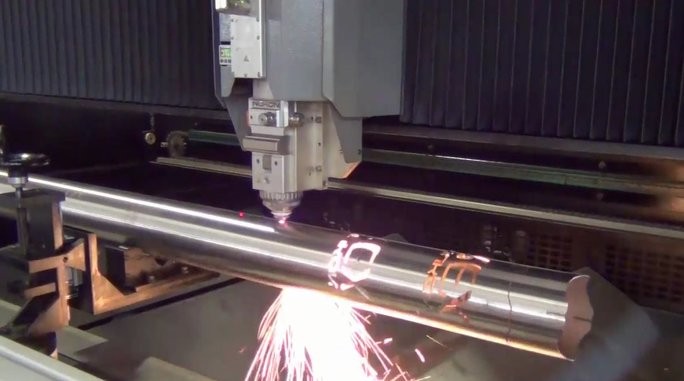
For precision fabricated parts and components, laser metal cutting is ideal. Thanks to advances in technology, the best laser metal cutting machine manufacturers can create just about anything to exact specifications. Because of that, they serve customers from all industries, including automotive, aerospace, food processing, mining, aviation, and medical.
Although aluminum laser cutting is in most demand, a top fabricator has state-of-the-art machinery capable of cutting heavy plate, galvanized steel, stainless steel, and other metals. By directing a high-powered laser in conjunction with CNC machining, you end up with a perfect finished product or one prepared for a further manufacturing process.
Compared to more traditional cutting options, sheet metal laser cutting is more advantageous. Some of the advantages include the following:
- Accuracy – Especially for stainless steel, mild steel, and aluminum laser cutting, the process is extremely accurate. The focused laser can cut precisely detailed shapes, as well as small lines and holes. Remember, even one small defect could be enough to cause serious problems. Not only could it damage the customer’s reputation as a viable business, but when using components as part of a manufacturing process, it could seriously damage machinery.
- Clean Edges – The edge quality with laser cutting is unbeatable. Because the laser beam experiences no wear throughout the cutting process, has intense focus, and requires less heat than other cutting methods, the edges of the metal workpiece always come out clean. Following a narrow path known as the “heat affect zone,” the beam cuts parts with incredible precision, with clean edges, and to a higher tolerance.
- No Cutting Tool Costs – Laser cutting does not require hand tools. That eliminates the need for changeovers, storage, and sharpening. Ultimately, there are no tooling costs, saving the customer money.
- Repeatable Performance – Perhaps one of the biggest advantages of laser cutting is that this process offers repeatable performance. In other words, high-tech equipment can produce perfectly replicated finished products.
- Enhanced Speed – For customers with tight deadlines, the laser cutting method is an excellent solution. Again, compared to traditional cutting, a reputable fabricator can complete projects faster.
- No Warping – Due to the high speed of laser cutting, which results in a small heat affect zone, and the fact that the beam never touches the metal, there is little, if any, distortion to the workpiece.
- Fewer Scraps – Today, an increasing number of industries look for eco-friendly solutions. Because there are fewer material scraps with laser cutting, it appeals to a broad range of customers. With this method, tabbing, lead-ins, lead-outs are additional ways to reduce scrap.
- Quick Setup – Without hard tooling, the setup process for laser metal cutting machine manufacturers decreases significantly. That further reduces the cost of laser cutting, which the fabricator can then pass on to the customer.
- Endless Possibilities – For customization, laser cutting provides endless possibilities.
Outstanding Fabrication Services
For the best metal fabrication services, call us at Weldflow Metal Products. We offer precision fabrication services at affordable prices.